Preventing Weld Undercut: Proven Techniques Every Welder Should Know
Preventing Weld Undercut: Proven Techniques Every Welder Should Know
Blog Article
Mastering the Art of Welding: Exactly How to Avoid Undercut Welding Issues for Flawless Construction Results
By comprehending the root creates of undercut welding and implementing effective techniques to prevent it, welders can raise their craft to new levels of excellence. In the quest of flawless manufacture outcomes, understanding the art of welding to stay clear of undercut issues is not simply a skill but a necessity for those striving for perfection in their work.
Comprehending Undercut Welding

To avoid undercut welding, welders must guarantee correct welding parameters, such as readjusting the current, voltage, travel rate, and preserving the proper electrode angle. Additionally, making use of the appropriate welding method for the details joint setup is crucial. Employing weaving movements or backstepping strategies can help make sure proper weld metal deposition and minimize the chance of undercut formation. Routine assessment of welds during and after the welding process is likewise critical to capture any undercut early and make needed changes to stop further problems. Preventing weld undercut. By recognizing the sources of undercut welding and implementing safety nets, welders can attain premium, structurally sound welds.
Reasons For Undercut in Welding
Understanding the factors that add to damage in welding is important for welders to create top quality, structurally audio welds. Inadequate welding present or wrong welding speed can additionally contribute to undercut. Understanding these causes and implementing appropriate welding methods can assist prevent undercutting problems, ensuring sturdy and strong welds.
Strategies to stop Undercutting

To mitigate the threat of undercutting in welding, welders can employ strategic welding strategies aimed at improving the top quality and honesty of the weld joints. Furthermore, making use of the correct welding technique for the particular joint setup, such as weave or stringer grains, can contribute to lowering damaging.
Using back-step welding strategies and controlling the weld bead profile can also assist disperse warm equally and lessen the threat of undercut. Routine assessment of the weld joint during and after welding, as well as carrying out top quality guarantee actions, can assist in addressing and finding undercutting problems promptly.
Significance of Proper Welding Specifications
Selecting and keeping proper welding criteria is essential for accomplishing successful welds with marginal defects. Welding parameters refer to variables such as voltage, current, take a trip rate, electrode angle, and securing gas circulation rate that straight impact the welding procedure. These parameters have to be meticulously changed based on the sort of product being welded, its density, and the welding technique utilized.
Correct welding specifications ensure the best quantity of warm is related to thaw the base steels and filler product consistently. If the criteria are set expensive, it can bring about extreme warmth input, triggering spatter, burn-through, or distortion. On the check my source various other hand, if the specifications are as well low, insufficient fusion, absence of infiltration, or damaging might take place.
Quality Control in Welding Workflow
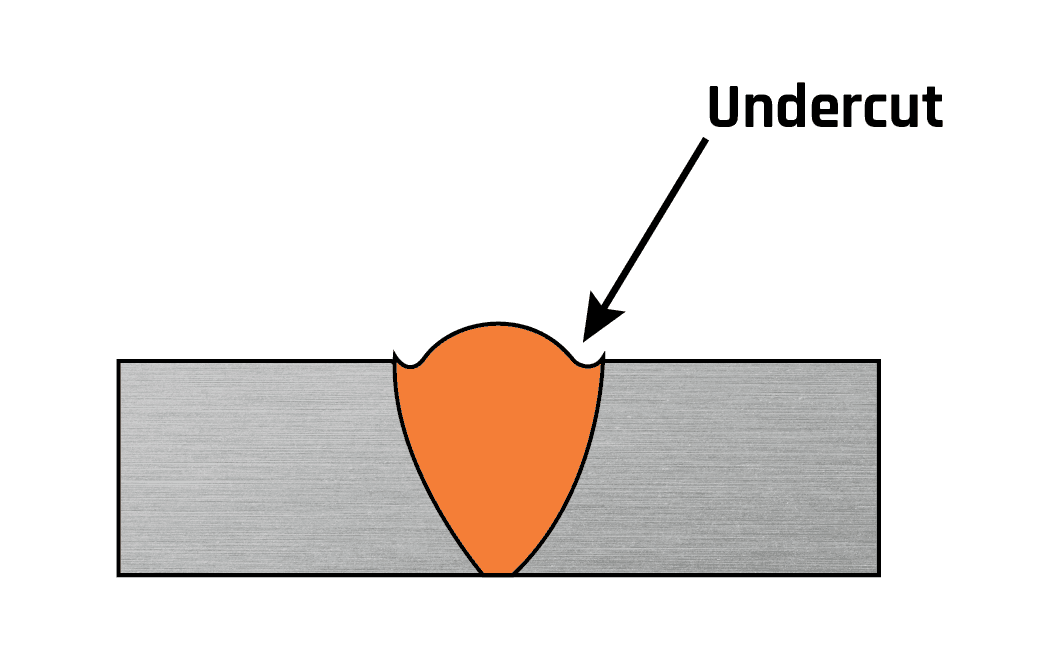
Final Thought
Finally, grasping the art of welding requires a detailed understanding of undercut welding, its causes, and techniques to stop it. By making sure appropriate welding criteria and implementing quality control methods, perfect manufacture results can be attained. It is necessary for welders to consistently make every effort for excellence in their welding procedures to stay clear of undercut concerns and generate high-grade welds.
Undercut welding, a typical issue in welding procedures, occurs when the weld metal does not effectively load the groove and leaves a groove or clinical depression along the bonded joint.To stop undercut welding, welders need to ensure appropriate welding criteria, such as changing the present, voltage, traveling speed, and preserving the right electrode angle. Poor welding inaccurate or current welding rate can also add to undercut.To minimize the risk of damaging in welding, welders can utilize tactical welding methods intended at boosting site the high quality and integrity of the weld joints.In final thought, understanding the art of welding calls for a detailed understanding of undercut welding, its reasons, and techniques to prevent it.
Report this page